
What is a Mounted Point?
Mounted Point is a very small bonded abrasive or superabrasive tool with a ball, point, cone, cylinder, or bullet shape. This high abrasive tools are designed for portable die grinder and deburring in which the tool in mounted on a pin or mandrel. Mounted point is famous for different applications such as dry grinding, wet grinding, material removal or roughing, etc. Together with other abrasive tools, it also comes in various product specification where each mounted point has its own unique application, tool performance, and benefits. Let this blog page guide you in choosing the right mounted point for your work.
Mounted Point Selection Guide
Product Specification
To make the most out of any tool, you have to choose the right size, shape, grain type, bond type, applications, and performance parameters. That is the sole purpose of this blog.
Abrasive Grain Type
When it comes to mounted point, you have to choose the perfect grain type for your work application. Mounted Points grain type include aluminum oxide, cubic boron nitride, ceramic, silicon carbide, alumina zirconia, tungsten carbide, and other abrasive grains with a metal layer. In general, two main grain types are likely to use by professionals. Those are the aluminum oxide (A) and silicon carbide (SIC).
Here's a more defined description of according to ISO 525. Make use the abbreviations to specific and identify the grain mixtures.
Abbreviation | Grain Mixture |
AD | Aluminum Oxide, dark red |
AW | Aluminum Oxide, white |
AR | Aluminum Oxide, pink |
AN | Aluminum Oxide, regular |
AH | Bubble grain aluminum oxide |
CN | Silicon carbide, green |
CU | Silicon carbide, grey |
CO | Ceramic oxide grain |
ADW | Aluminum oxide mixture ( AD + AW ) |
ARN | Aluminum oxide mixture ( AR + AN) |
ADR | Aluminum oxide mixture ( AD + AR) |
AWCO | Aluminum oxide mixture ( AW + CO) |

Grain Size and Shape
Mounted point sizes and shapes usually follow a certain standard. Common mounted points abide the ANSI, FEPA, or JSI grain size standards, though there are some available micron-graded products which are considered fine abrasive grains graded to micron sizes based on average particle size.
Mounted Point Shape Chart
To have full access to the area you are working on, you have to pick the right shape especially for burrs and sharp edges with hard-to-reach areas. Mounted points come in various shapes from A to W which fits many different applications.
Here’s a sample shape chart for your reference.
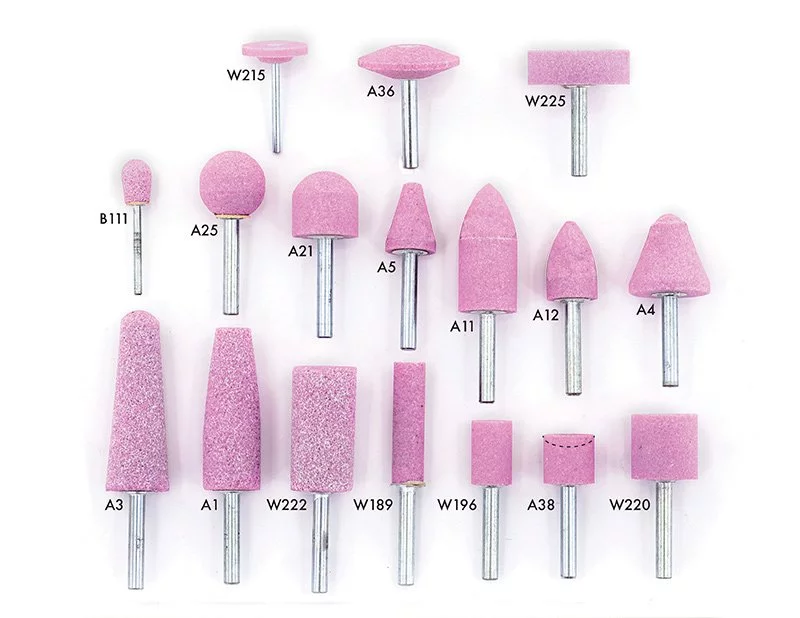
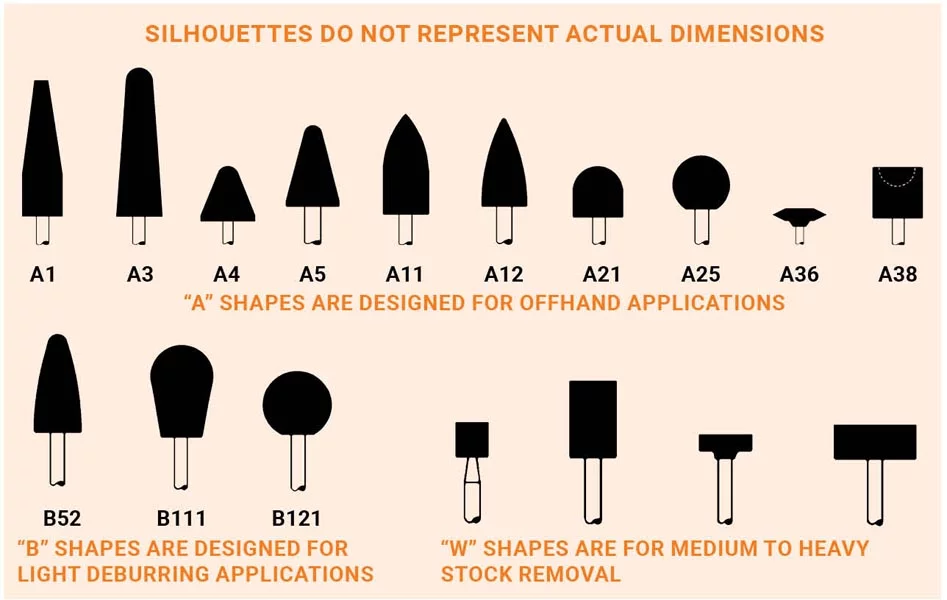
Performance Parameters
Mounted points performance rate depends on the rotary speed, shank diameter, or bore inner diameter (ID), and outer diameter (OD). The center mount of this abrasive tool in the bore inner diameter which is use to mount or hold the abrasive on a spindle or mandrel. On the other hand, the shank diameter is the internal shank, pin, shaft, or mandrel on mounted points or wheels.
- Shanks
Shank Diameter | Shank Length |
Shank diameter 3 mm | 30 mm shank length |
Shank diameter 6 mm | 40 mm shank length |
Shank diameter 8 mm | 40 mm shank length |
Shank diameter 1/8” | 1 1/4 shank length |
Shank diameter 1/4” | 1 1/2” shank length |
- Rotational Speed
Refer to the table below for the recommended rotational speed based on the diameter and cutting speed based on the diameter and cutting speed of your tool.
Note: The optimum rotational speeds can be found in the table. The speed is limited to 150,000 RPM. This is because conventional drives do not permit a higher RPM.
Mounted Point diameter (mm) | Cutting Speed (m/s) | ||||||
10 | 15 | 20 | 25 | 30 | 40 | 50 | |
Rotational Speed (RPM) | |||||||
2 | 95,500 | 143,200 | 191,000 | 238,700 | 286,500 | 382,000 | 477,500 |
3 | 63,700 | 95,500 | 127,300 | 159,200 | 191,000 | 254,600 | 318,300 |
4 | 47,700 | 71,600 | 95,500 | 119,400 | 143,200 | 191,000 | 238,700 |
5 | 38,200 | 57,300 | 76,400 | 95,500 | 114,600 | 152,800 | 191,000 |
6 | 31,800 | 47,700 | 63,700 | 79,600 | 95,500 | 127,300 | 159,200 |
7 | 27,300 | 40,900 | 54,600 | 68,200 | 81,900 | 109,100 | 136,400 |
8 | 23,900 | 35,800 | 47,700 | 59,700 | 71,600 | 95,500 | 119,400 |
10 | 19,100 | 19,100 | 38,200 | 47,700 | 57,300 | 76,400 | 95,500 |
12 | 15,900 | 23,900 | 31,800 | 39,800 | 47,700 | 63,700 | 79,600 |
14 | 13,600 | 20,500 | 27,300 | 34,100 | 40,900 | 54,600 | 68,200 |
16 | 11,900 | 17,900 | 23,900 | 29,800 | 35,800 | 47,700 | 59,700 |
20 | 9,500 | 14,300 | 19,100 | 23,900 | 28,600 | 38,200 | 47,700 |
25 | 7,600 | 11,500 | 15,300 | 19,100 | 22,900 | 30,600 | 38,200 |
32 | 6,000 | 9,000 | 11,900 | 14,900 | 17,900 | 23,900 | 29,800 |
40 | 4,800 | 7,200 | 9,500 | 11,900 | 14,300 | 14,300 | 23,900 |
50 | 3,800 | 5,700 | 7,600 | 9,500 | 11,500 | 15,300 | 19,100 |
Grit Size and Grating System
The grit size will depend on the amount of metal you want to remove. To choose the right grit size, you have to remember that the lower the grit number, the coarser the grain can be. If you are into faster stock removal, then selecting a coarse grit would be a great idea. If you are working on light deburring, edge-breaking, and blending, better select a finer grit for best result. The standard grit size depends on the shape and diameter of the tool. In general, a grit size of 30 is often used for various applications.
Here’s a standard hardness grade according to ISO 525. These are classified using alphabetical letters to specify the hardness from soft to hard level. The mounted point on the right side is an example of a hardness grade M (Medium)
Hardness Grade Coding | Property | |||
A | B | C | D | Extremely Soft |
E | F | G | - | Very Soft |
H | I | J | K | Soft |
L | M | N | O | Medium |
P | Q | R | S | Hard |
Y | U | V | W | Very Hard |
X | Y | Z | - | Extremely Hard |
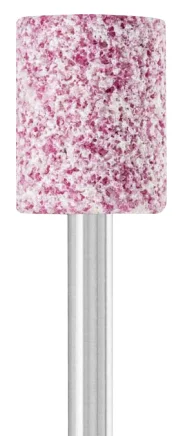
Hardness K – manufactured from a grain mix of pink aluminum oxide and regular aluminum oxide in a vitrified bond. This grain combination provides good stock removal and long service life. This hardness grade is often used for general use on cast iron parts

- Hardness F – This hardness grade is manufactured from green silicon carbide in a vitrified bond. The good thing about this is that there is a microstructure and special impregnation that allows high stock removal rates when you are working on soft and greasy materials. This is often characterized with high abrasive qualities used commonly for aluminum and non-ferrous metals.
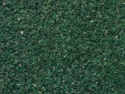
- Hardness D – This hardness grade is manufactured from a special vitrified bond and bubble grain aluminum oxide. This low bond volume combination produces the softest mounted points with its easy-to-break down bubble grain. In general, a hardness D is suitable for soft materials such as plastic, rubber and wood, which is characterized by high abrasiveness.
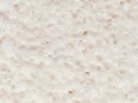
- Hardness M – This hardness grade is made on a mixture of dark red and white aluminum oxide grit in a vitrified bond. Among the different hardness grade, M is the most aggressive one. If you are likely to use your mounted point for general use especially with high abrasive and stock removal rates, choose this hardness grade.

- Hardness O – This hardness grade is composed of pink aluminum oxide in a vitrified bond. This is often known for its good edge holding and long service life which makes it predominant in its field of application.

- Hardness J – A mixture of white aluminum oxide and blue ceramic sintered aluminum oxide in a vitrified bond. This type of hardness is suitable for surface work on titanium materials, nickel and cobalt-based alloys. Hardness J has self-sharpening effect and easy-to-break down with its soft bond combination.

- Hardness L – This is a combination of a white and dark red aluminum oxide in a high-quality resin bond. Among the different hardness grade level, Hardness L is considered as a fairly soft bond achieving a very good removal rate.

- Hardness N – This is made up of a regular aluminum oxide in a high-quality resin bond. This hardness grade is known for its elevated hardness and durability. Heavy duty grinding on stainless steel used this hardness grade which is notable for high edge-holding capability, long service life and low wear resistance.

Bond Type
Selecting the bond type is an important factor in removing stocks on metals. Softer bonds work best on harder metals, while harder bonds is recommended for soft metals. Various bond types like vitrified and resinoid is often use for an array of application use in both surface and edge grinding. These bond types can be used on a variety of materials from stainless steel and cast iron to exotic alloys.
Rubber bond types are often used in edge breaking applications. This is done by removing the edge of a stainless-steel sheet metal before fabrication process.

For aluminum bonds, look for a non-loading bond since aluminum has a low melting point and it can load up the abrasive product you are operating with. Metal bond types are used mainly for superabrasive or tungsten carbide grit products. For silicate or oxychloride bond systems, use it if you are looking for a low-strength bonds that keep heat generation to minimum. But if you’re looking for a much durable and hard quality bond, try to use vitrified and resin bond types.
Applications
Mounted points can be used in many different applications such as dry grinding, wet grinding, material removal or roughing, blending or intermediate cutting, or finishing and deburring. There are also other mounted points used for polishing, honing, cylindrical or centerless grinding, form or gear grinding, bench or backstand grinding, or portable grinding.

The application must be selected according to the type of work on the material that will be used. The bond type and grain mixture will surely create a big impact on the grinding output. You can classify the application based on three categories:
- General Use. The application part focuses on balance between grinding output and service life.
- Surface Grinding. The mounted points are subject to lower loads. This is why the mounted point bond is quite soft and is regularly designed to give high stock removal.
- Edge Grinding. Mounted points used for edge grinding must be dimensionally stable. That is why the mounted point bond is comparatively hard and is created to provide long service life.
Mounted points are used in wide range of application on various places. Here are just few of them:
- Aerospace (Jet Engine Turbine Blades) – If you are fond of aerospace, you often see propellers whirring away as you hear the dull roar of the engine. Those components are finished and repaired regularly using mounted points. The highly intricate and often angular shaped metal of mounted points is used for aeroplane jet engine blades.
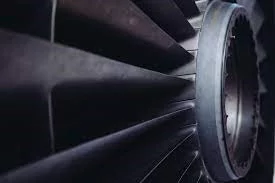
- Dental and Medical Instruments – Medical tools used by dentist for poking, prod, and picking your teeth is ground and finished with a mounted point. Likewise, medical and surgical equipment and instruments is grounded by these mounted points. From orthopedic hammer to highly complex workpiece like the metal hip replacement, mounted points offer high precision, accuracy, and versatility.
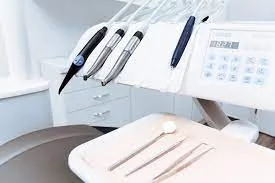
- Oil Drilling – Mounted points is also used for creating drill heads which are used in the extraction of oil and natural gas. The drill heads should undergo interior diameter grinding which is also subject to complex arrangement of tooth and cone shapes built to remove materials in the ocean floor. With its high complexity, using mounted points is the most preferable thing so we can reach those hard-to-reach areas.

- Tool Casts and Hardware – You may not know it but the tool casts and moulds in your work station is maintained and finished by abrasive mounted points. Moulds are complicatedly shaped, thus needs a precision abrasive such as mounted points to repair them.

Other Related Applications
- Drive Spindle Extensions. Oftentimes, mounted points with a shank diameter of 3, 6, and 8 mm can be extended with a drive spindle extension. This is made for the sole purpose of accessing the hard-to-reach areas. It is mounted in the collet of the tool drive like the air grinder and electric grinder, or mounted in the handpiece of the flexible shaft.
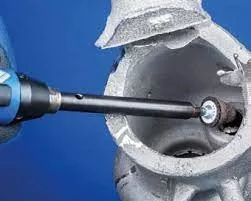
Mounted point has a wide range of product specification, features, and application suitable for specific needs. We hope this selection guide will help you choose the perfect mounted point for your work. To know more about mounted point types, grinding wheels, and abrasive accessories, visit our page agrindtool.com