What is Truing?
Before we get to know the whole process of how to true a diamond grinding wheel, we have to know first the concept of truing. Truing is the process of modifying the shape of a grinding wheel when it wears away from its original shape due to abrasive and bond breakage. It is done to make the wheel's perimeter concentric with its axis and its side true, in order to restore the face's lost shape.
The form or profile of the grinding wheel is the subject of truing operations. The grinding face of a new abrasive wheel is adjusted during truing to allow the abrasive product to perform what it needs to do. During the grinding process, routine truing corrects the wheel profile and accounts for form loss as the wheel wears down. A correctly trued wheel will impart the proper profile to the item being ground, as well as ensure that the form geometry and dimensioning are accurate and ready to use.
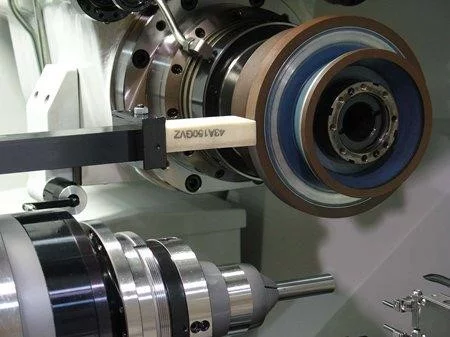
Truing vs Dressing
Most people thought that truing and dressing are just the same, especially when it comes to the grinding wheel. That is because truing and dressing can be done or applied at the same time. For an instance, some resin and metal bonded products are trued offline and can be dressed afterward. But it is very important, that you know its differences. The two terms involve different processes.
Truing deals with the form of the grinding wheel. During routine truing on a grinding application, the wheel’s profile or form is being corrected as it compensates for the loss forms, especially when the wheel broke down. This is to ensure that the geometrical form and dimensioning specs are ready for their next application.
On the other hand, dressing is done to restore or alter the condition of the wheel’s surface. Dressing deals with restoring the ability of the wheel to remove stock and generate a great surface finish. How does restoring being done? The grinding face of the wheel is dressed by exposing new and sharp cutting points that will allow the wheel to perform a high material removal rate. Now that you've learned the difference between dressing and truing, let us now focus on the process of how to true a diamond grinding wheel.Â
How to True a Diamond Grinding Wheel?
Trueing takes place on glazed wheels. The act of restoring the cutting face of a grinding wheel by removing abrasive material from the cutting face and sides of the wheel so that it runs true with regard to the axis of rotation and produces perfect round or flatwork is known as wheel truing.
To guide you on how to true a diamond grinding wheel, here are some of the more frequent methods that are commonly used by experts.
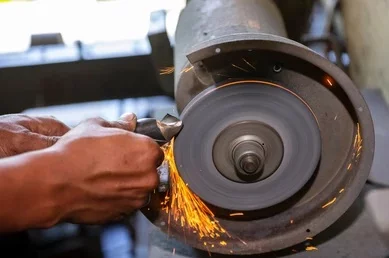
Mild Steel Block
Truing Procedures:
- In this method, using a grinder, carefully place a mild steel block.
- Make a couple of passes across the steel block. Per pass, O.OOl-in. (O.02-mm) depth
- Check the wheel face or turn off the grinder. Truth circumference with a dial indicator
- Continue passing over the steel if necessary. Block the wheel until the runout is gone.
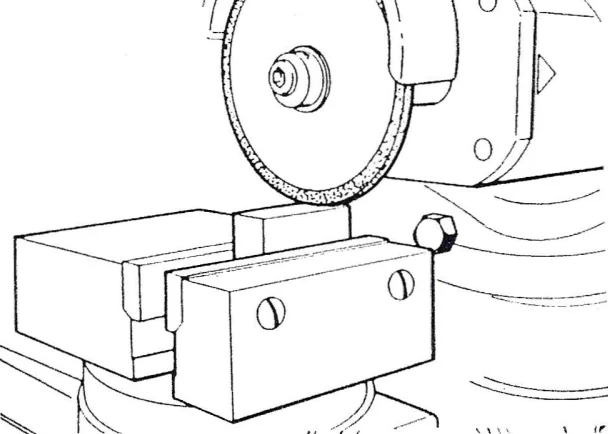
Dresser with Brake
Another alternative that you can do on how to true a diamond grinding wheel is through the use of a dresser. This is usually used for truing various types of grinding wheels like the Diamond and CBN grinding wheel (1A1 Straight Wheels, 1A1R Cut off wheels, Mounted and un-mounted internal grinding wheels, 1V1 angle wheels, 11V9 Cup wheels, and Core drill outer diameters)
Truing Procedures:
- Set up the truing tool properly then bring the diamond grinding wheel into the truing wheel.
- Run the diamond grinding wheel at an operating speed. Start the truing process by letting the truing wheel spin in the same direction of rotation as the diamond grinding wheel.
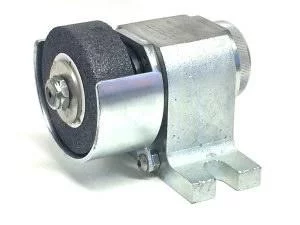
- You have to make sure that the truing tool is mounted. This is to keep the tool paralleled like that of a peripheral wheel type or perpendicular to a cup wheel type.
- The truing wheel should run off the diamond wheel to avoid it from chipping the edges.
- For the truing wheel speed, the general or average truing operations are between 1000 and 1500 surface feet per minute. You have to make sure that the speed is just enough for the wheel. Too much can lead to a lack of truing wheel wear, which is essential in the truing process. While too low speed might lead to excessive wear of the grinding wheel.
- You can adjust the truing speed using the brake shoes through the following options:
- If you will turn in the screws the spindle should have a maximum of 1500 S.F.P.M
- If the screws are turned out, the spindle should have two revolutions with a minimum speed of 1050 S.F.P.M.
- If you turned it out against the screw, the spindle should have one revolution in the current setting
- The next step is to make the wheels in contact with each other while the truing wheel is continuously spinning. Do this by passing one wheel back and forth across the face of the diamond grinding wheel at a rate of 30 to 60 inches per minute.
- Check if the trimming operation is completed.
Super Double Diamond Dresser (S.D.D.D)
These truing tools are considered major innovations in the diamond grinding wheel truing process because of their exotic metal formulations that provide excellent truing action compared to the other truing methods. This tool is usually used on straight wheels, angled wheels, and other diamond wheels. Here are the procedures on how to true a diamond grinding wheel using a super double diamond dresser.Â
Truing Procedures:
- Place the truing tool in the holder then exposed the S.D.D.D tool on a scale of not more than ½.
- To observe a better active sparking interface, you can turn off your working light. You may also turn off the coolant.
- Next is to set up the feed to let the tool move from a moderate to a fast level speed. In this part, you may expect active sparking interface effects.
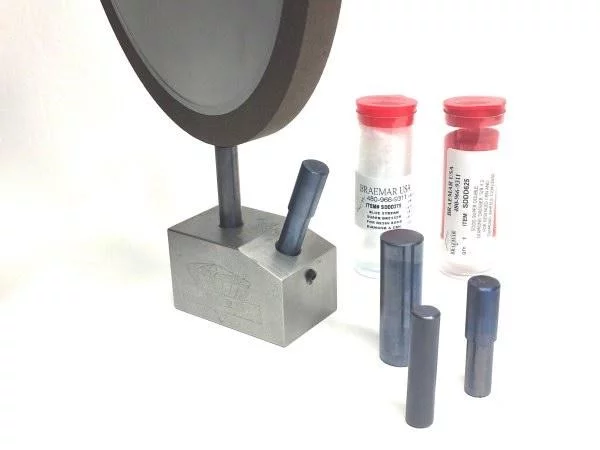
- For the fourth step, it is better to set up the down feed using a feed chart. Remember, it is very important to check your feed. The correct feed is determined by the hardness and grit size of the wheel.
- The down feed should be higher to true the wheel. Low-down feed will simply wear out the S.D.D.D tool without any truing changes in your diamond grinding wheel.
- Move the dresser in several passes. Avoid truing in one direction as it may lead to the crown formation on your grinding wheel.
- Lastly, after doing 3 passes across the wheel, you may reduce the down feed. This will result in a trued wheel that has outstanding cutting performance on any workpieces. It will also leave an excellent and correct surface finish.
Grinder for Toolposts
If you have a toolpost on your workshop, this can be an alternative method on how to true a diamond grinding wheel.
Truing Procedures:
- On the grinder table, mount a toolpost grinder.
- Install a vitrified silicon carbide grit of 80 to 120 grit wheel on the grinder spindle to spin at about a fraction of its regular speed
- Set up the silicon carbide and diamond wheel. To operate in opposite directions, turn the wheel.
- Make a few 0.001 in passes (0.02 mm) over the wheel of diamonds
- With a dial indicator, check the wheel for runout.
- Carry on passing over the diamond until the runout has been addressed.
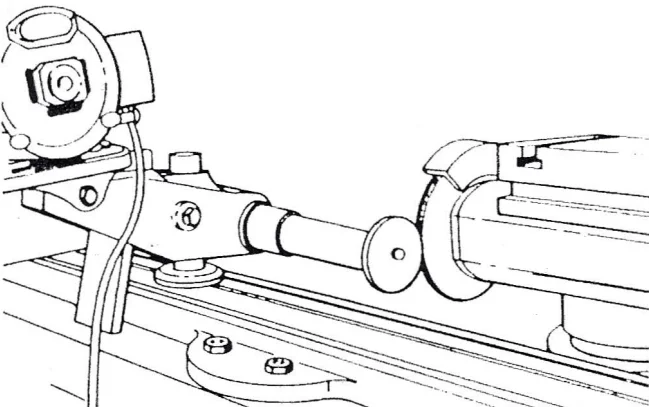
The appropriate truing tool cannot be easily picked without any basis. To make sure you are using the correct truing tool for your diamond grinding wheel, you have to check if it coordinates well with the structure and properties of your wheel. Here’s a list of tool selection considerations that you have to follow before choosing your truing tool.
Â
How to Choose the Appropriate Truing Tool?
To make sure that you are on the right track and you are following the correct process on how to true a diamond grinding wheel, check out these important tips on choosing the appropriate truing tool.Â
- Abrasive wheel like diamond grinding wheels has their own sizes, bond, and abrasive types. You have to know these characteristics since you will also base here the size of your diamond material to be trued.
- Know the form or profile required on the diamond grinding wheel. There are lots of stationary tools that can be used in the restoration or truing process. A stationary tool can be as simple as a diamond stick. Whatever stationary tools you have chosen, you have to understand their characteristics and limitations because that will help you in knowing what to do and what can you do.
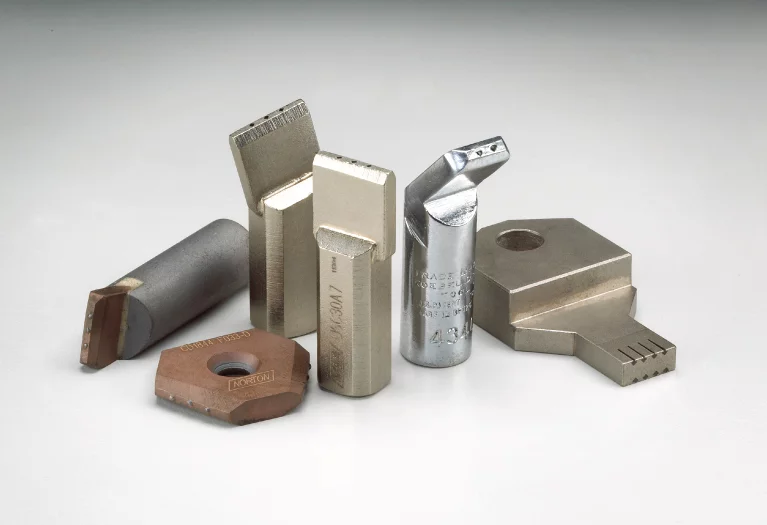
- The last consideration is the quality of the diamond tool. Although high-quality diamonds are quite expensive, you can assure of their quality especially when it comes to durability, inclusions, cracks, and imperfections. A higher-quality diamond tool will always have more defined points compared to low-quality diamond materials.
Â
Is Truing Necessary?
Truing is necessary for precision grinding since it ensures that the grinding wheel's contact face is shaped to run perfectly true to the task. Chatter marks will appear on an out-of-true wheel. To guarantee correct wheel face truing, make sure the diamond is aligned with the grinding wheel's horizontal centerline. The grinding wheel is then passed extremely slowly across the diamond, taking only a few thousandths of a millimeter at a time. A cut of one thousandth or less should be utilized with a very slow traverse for finer finishing.
All abrasive products are susceptible to breaking forms and structures. That is why, through the truing method, we can restore the grinding wheel to its optimum state where it can again perform a high level of grinding work. There are still lots of things to learn on how to true a diamond grinding wheel. But we really hope that this blog helps you in one way or another. To know more about various truing tools, visit our website at agrindtool.com.For more truing and dressing tools details, check out our blog on "How to use a diamond dresser to dress and true grinding wheel".Â
Â